Explanation of the basic operation and principles
Manual Metal Arc (MMA) welding, also known as Shielded Metal Arc Welding (SMAW), is one of the most widely used welding processes globally. The fundamental principle of an MMA welding machine is based on the generation of an electric arc between the electrode and the workpiece. This electric arc serves as the heat source, melting both the electrode and the base metal, which then solidify to form a strong joint.
When the MMA welding machine is turned on and the electrode is brought close to the workpiece, a high voltage is applied to ionize the air gap between them. Once the air is ionized, it becomes conductive, allowing an electric current to flow, creating the arc. The temperature of this arc can reach extremely high levels, typically around 6000 - 7000°C, which is sufficient to melt the metals involved.
The electrode used in MMA welding is coated with a flux material. As the electrode melts, the flux burns and decomposes, producing a protective gas shield around the weld pool. This gas shield protects the molten metal from atmospheric contaminants such as oxygen and nitrogen, which could otherwise cause porosity and other defects in the weld. Additionally, the flux also forms a slag layer on top of the solidified weld bead. This slag acts as an additional protective layer during the cooling process and can be removed after the weld has cooled down, revealing a clean and smooth weld surface.
Key components and their functions
- Power supply unit: This is the heart of the MMA welding machine. It converts the incoming electrical power (usually from a mains supply) into the appropriate voltage and current levels required for welding. The power supply can be either a transformer-based unit or an inverter-based unit. Transformer-based power supplies are more traditional, using electromagnetic principles to step down the voltage and increase the current. Inverter-based power supplies, on the other hand, are more modern and efficient. They first convert the incoming AC power to DC, then use electronic circuits to rapidly switch the current on and off, creating a high-frequency output. This high-frequency output is then stepped down to the desired welding voltage and current. Inverter-based machines are generally lighter, more compact, and offer better control over the welding parameters.
- Electrode holder: As the name suggests, the electrode holder is used to grip the welding electrode. It is designed to conduct electricity from the power supply to the electrode. The electrode holder must be able to maintain a good electrical contact with the electrode to ensure a stable arc. It also needs to be insulated to protect the welder from electrical shock. Most electrode holders have a spring-loaded mechanism to securely hold the electrode and allow for easy replacement when the electrode is consumed.
- Workpiece clamp: The workpiece clamp is connected to the other terminal of the power supply and is attached to the workpiece being welded. Its function is to complete the electrical circuit, allowing the current to flow from the power supply, through the electrode, the arc, and back to the power supply via the workpiece. Similar to the electrode holder, the workpiece clamp must provide a good electrical connection to the workpiece. It should be firmly attached to a clean and unpainted surface of the workpiece to ensure a stable current flow.
- Control panel: The control panel of an MMA welding machine allows the welder to adjust various parameters such as the welding current. By increasing or decreasing the current, the welder can control the heat input, which in turn affects the penetration depth, bead width, and the overall quality of the weld. Some advanced MMA welding machines may also have additional controls for features like hot start (which provides a momentary increase in current to start the arc more easily) and anti-stick (which reduces the tendency of the electrode to stick to the workpiece).
2. Key Features to Look for in an MMA Welding Machine
Power output and duty cycle
- Power output: The power output of an MMA welding machine is typically measured in amperes (A). It determines the amount of current that can flow through the welding circuit, which directly influences the heat generated at the weld site. Different welding applications require different levels of power output. For thin sheet metal welding, a lower current in the range of 30 - 60 A may be sufficient, while for thicker metals, currents ranging from 100 A to several hundred amperes may be needed. When choosing an MMA welding machine, it is important to consider the thickest material you are likely to weld. A machine with a higher maximum power output will be more versatile and able to handle a wider range of projects. However, it is also important to note that higher power output machines may consume more electricity and require a more robust electrical supply.
- Duty cycle: The duty cycle of an MMA welding machine is a crucial factor that indicates the machine's ability to operate continuously without overheating. It is expressed as a percentage and is defined as the ratio of the time the machine can be used at a given current level within a 10 - minute period. For example, a machine with a 60% duty cycle at 200 A means that it can be used for 6 minutes out of every 10 minutes at a current setting of 200 A. After this period, the machine needs to cool down to prevent damage. Machines with a higher duty cycle are more suitable for heavy - duty applications where continuous welding is required, such as in industrial manufacturing settings. In contrast, machines with lower duty cycles may be sufficient for occasional or light - duty welding tasks, like home DIY projects.
Portability and ease of use
- Portability: The portability of an MMA welding machine is an important consideration, especially for welders who need to work in different locations. Transformer-based machines are generally larger and heavier due to the presence of bulky magnetic cores. Inverter-based machines, on the other hand, are much lighter and more compact, making them easier to transport. Some inverter-based MMA welding machines are even designed to be as small as a briefcase, allowing welders to carry them around with ease. Additionally, the weight and size of the machine also affect its maneuverability within a workspace. A more portable machine can be moved around more easily to access hard-to-reach welding areas.
- Ease of use: An MMA welding machine should be easy to operate, even for beginners. The control panel should be intuitive, with clearly labeled buttons and dials for adjusting the welding parameters. Machines with digital displays are becoming increasingly popular as they provide more accurate and easy-to-read information about the welding settings. The electrode holder and workpiece clamp should be easy to attach and detach, and the overall design of the machine should be ergonomic to reduce fatigue during long welding sessions. Some machines also come with features like automatic shut-off after a period of inactivity, which not only saves energy but also enhances safety.
Safety features and certifications
- Safety features: MMA welding machines should be equipped with a variety of safety features to protect the welder from potential hazards. One of the most important safety features is electrical insulation. The machine's casing, electrode holder, and other components should be well-insulated to prevent electrical shock. Overload protection is also crucial, as it shuts off the machine if the current exceeds the rated capacity, preventing damage to the machine and reducing the risk of electrical fires. Thermal protection is another important feature, especially in machines with high duty cycles. It monitors the temperature of the machine's internal components and shuts off the machine if it overheats. Some machines also have anti - splash guards and fume extraction systems to protect the welder from flying sparks and harmful fumes.
- Certifications: When purchasing an MMA welding machine, it is important to look for certifications that ensure the machine meets international safety and quality standards. Certifications such as CE (Conformité Européene) in Europe and UL (Underwriters Laboratories) in the United States indicate that the machine has been tested and approved by independent organizations. These certifications provide assurance that the machine is safe to use and complies with relevant regulations.
Certification
|
Region
|
Significance
|
CE
|
Europe
|
Indicates compliance with European health, safety, and environmental protection standards
|
UL
|
United States
|
Verifies that the product meets safety requirements set by Underwriters Laboratories
|
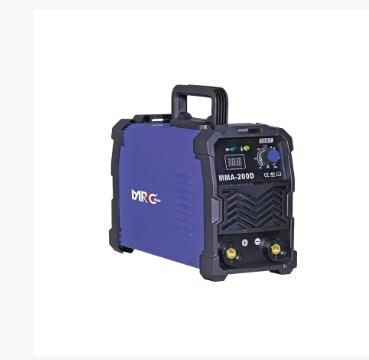
3. Common Applications of MMA Welding Machines
Industries and projects where MMA welding is preferred
- Construction industry: In the construction industry, MMA welding is widely used for various applications. It is used for welding structural steel components in buildings, bridges, and other large - scale structures. The ability of MMA welding to work in different positions (flat, vertical, horizontal, and overhead) makes it suitable for on - site welding where access may be limited. For example, when erecting a steel frame for a building, welders can use MMA welding machines to join the beams and columns together. MMA welding is also used for welding pipes and other metal components in plumbing and HVAC systems.
- Shipbuilding industry: Shipbuilding requires the joining of large and thick metal plates. MMA welding is often the preferred method due to its high - heat - input capabilities, which can achieve deep penetration in thick metals. It is used for welding the hull plates, bulkheads, and other structural components of ships. The portability of MMA welding machines also makes them suitable for use in the confined spaces and challenging environments found on ships during construction and repair.
- Repair and maintenance: MMA welding is extremely useful for repair and maintenance work. Whether it's fixing a broken metal part on a vehicle, repairing a damaged machine in a factory, or patching up a metal structure, MMA welding can be quickly set up and used. The wide range of electrodes available allows welders to match the electrode to the material being repaired, ensuring a strong and reliable repair. For example, in the automotive industry, MMA welding can be used to repair chassis components, exhaust systems, and body panels.
- Art and sculpture: In the field of art and sculpture, MMA welding offers artists the freedom to create unique and complex metal artworks. The process allows for precise control over the welding process, enabling artists to create different textures and shapes. The ability to work with different types of metals and the portability of the equipment make it a popular choice for metal sculptors who may need to work on - site or in different studios.
Material compatibility (steel, iron, etc.)
- Steel: MMA welding is highly compatible with various types of steel. Mild steel, which is the most commonly used type of steel, can be easily welded using MMA welding. The appropriate electrode selection depends on the thickness of the steel and the required strength of the weld. For example, E6013 electrodes are commonly used for thin - to medium - thickness mild steel in all welding positions due to their easy - starting and smooth - running characteristics. For thicker mild steel, electrodes like E7018, which offer higher strength and better crack resistance, are often preferred.
- Stainless steel: MMA welding can also be used for welding stainless steel. Special electrodes with the appropriate chemical composition are used to ensure that the weld has the same corrosion - resistant properties as the base metal. For example, 308L electrodes are commonly used for welding 304 and 304L stainless steel. When welding stainless steel, it is important to control the heat input to prevent excessive grain growth and to maintain the corrosion resistance of the material.
- Cast iron: Cast iron can be welded using MMA welding, although it requires more careful preparation and selection of electrodes. Preheating the cast iron before welding helps to reduce the risk of cracking due to the high carbon content of the material. Specialized cast iron electrodes, such as nickel - based electrodes, are used to achieve a good weld joint. The welding process needs to be carried out slowly, and the weld should be allowed to cool slowly to prevent cracking.
Material
|
Recommended Electrodes
|
Welding Considerations
|
Mild steel
|
E6013, E7018
|
Depends on thickness; proper electrode selection for strength
|
Stainless steel
|
308L, 316L
|
Control heat input; match corrosion resistance
|
Cast iron
|
Nickel - based electrodes
|
Preheat; slow welding and cooling
|
4. Maintenance and Best Practices for MMA Welding Machines
Routine checks and upkeep
- Electrical connections: Regularly check all the electrical connections of the MMA welding machine, including the power cord, electrode holder cable, and workpiece clamp cable. Look for any signs of fraying, damage, or loose connections. Loose connections can cause arcing, which not only reduces the efficiency of the machine but also poses a safety hazard. Tighten any loose connections and replace any damaged cables immediately.
- Cooling system: If the MMA welding machine has a cooling system, such as fans or heat sinks, ensure that they are clean and free from dust and debris. A blocked cooling system can cause the machine to overheat, leading to reduced performance and potential damage. Clean the fans and heat sinks regularly using compressed air or a soft brush.
- Electrode holder and workpiece clamp: Inspect the electrode holder and workpiece clamp for wear and tear. Check the spring mechanism in the electrode holder to ensure that it is still functioning properly and can hold the electrode securely. Clean the contact surfaces of the electrode holder and workpiece clamp to remove any oxidation or dirt, which can increase electrical resistance and affect the welding process.
- Control panel: Wipe the control panel regularly to keep it clean and free from dust and moisture. Check that all the buttons, dials, and displays are functioning correctly. If any of the controls are not working properly, have the machine serviced by a qualified technician.
Tips for improving weld quality and machine longevity
- Proper electrode selection: Choosing the right electrode for the material and application is crucial for achieving good weld quality. Consider factors such as the type of metal, thickness, welding position, and required strength of the weld. Using the wrong electrode can result in poor fusion, porosity, and other weld defects.
- Maintain correct welding technique: A good welding technique is essential for producing high - quality welds. Keep the electrode at the correct angle (usually around 60 - 80 degrees to the workpiece), maintain a consistent arc length, and move the electrode at a steady speed. Practice different welding techniques for different positions to improve your skills.
- Avoid overloading the machine: Do not exceed the rated power output and duty cycle of the MMA welding machine. Overloading the machine can cause it to overheat and damage the internal components. If you need to weld for long periods at high currents, choose a machine with a higher duty cycle.
- Store the machine properly: When not in use, store the MMA welding machine in a dry, clean, and well - ventilated area. Protect it from moisture, dust, and extreme temperatures. If possible, cover the machine with a protective cover to prevent damage.
By understanding how MMA welding machines work, knowing the key features to look for, being aware of their common applications, and following proper maintenance practices, welders can make the most of these versatile and reliable welding tools, ensuring high - quality welds and a long - lasting machine.